Table of Contents
- What is a QMS?
- How QMS is beneficial for your business?
- Benefits of Quality Management Systems
- Why SharePoint is the best choice to create Quality Management System?
- 11 SharePoint Features You Need to Create a Quality Management System
- Start leveraging SharePoint QMS with BizPortals 365
Step into a smarter digital workplace
Get a Free Product TourA corporate environment is quite crowded with projects, people, processes, and many other matters at stake. This calls for a need to monitor and ensure everything stays on track.
And the best way to keep everyone and everything on track is an effective Quality Management System. The evolution of quality management has come a long way. It started with the defense sector followed by the automotive and marine sectors.
Today, the quality of products and services has become an integral part of business processes across the globe. Most organizations are adopting quality management systems to ensure customer retention and surpass their competitors in the market.
What is a QMS?
A Quality Management System is a formalized method to review products, services, and operations of the business. The key objective is to identify the scope of quality improvement. QMS is required in all aspects of the business, regardless of the nature and size of the organization.
Of course, getting compliance ready is the primary prerequisite for companies operating in a regulatory environment. However, the current challenges faced by quality managers highlight various deficiencies in business operations, people’s accountability, and a lack of visible or accessible data. In addition, due to lesser technological advancement, businesses usually get lodged in a time-consuming cycle of manual processing and complex document routing, jamming the entire quality process.
QMS, on the other hand, improves a company’s culture and its approach to quality by integrating employees, information, teams, and critical business processes. How? Let’s understand it with an example.
You definitely do not want your users to get a faulty product when you’re in the life science industry, particularly as a medical device manufacturer. In such a scenario, filing a deviation or change control form, getting it approved timely, and aligning it with your CAPA and training modules can be game-changing, not only to maintain product quality but also to improve your company’s bottom line. Read on to learn what a quality management process is and how digitalizing your overall quality process can save you dollars.
How QMS is beneficial for your business?
Implementing a Quality Management System offers tremendous benefits to your organization. In fact, a study found that the QMS implementation yields an average ROI of 300%. Other empirical studies confirm that businesses have also achieved non-measurable returns like happier customers, consistent operations, greater awareness of quality, and improved brand valuation.
Some of the critically important objectives of implementing a Quality Management System include regulatory risk, compliance, and certification. However, risk reduction is not the only benefit, but it can create a transformative impact on the company culture by creating a formalized system of processes.
Before we head to creating a robust quality management system in SharePoint, it’s critical to comprehend the quality procedures that need to be streamlined within the organization.
So, how does a QMS work? First, a QMS performs some core functions necessary to streamline your quality strategy. From filing an incident request to implementing corrective and preventive actions, it simplifies your overall quality management and training program by streamlining complex document routing and time-consuming approval processes. In addition, it constantly promotes process improvement and brings your team together on one page. If you’re looking to develop a flawless quality management strategy, it’s important to consider the following key aspects of quality management:
1. Incident management
An incident is primarily an occurrence that has the potential to disrupt business operations. From identification to analysis, and effective resolution of critical incidents are some of the primary functions of a QMS. It streamlines your incident management workflow for quicker, easier, and error-free form approvals, followed by CAPA initiation and implementation.
2. Deviation tracking and management
Every organization follows standard procedures and instructions to maintain the required regulatory environment. Deviation occurs whenever a process deviates from its established course. They can be planned (pre-approved) or unplanned (non-compliance with standard procedures). In both cases, a QMS helps you ensure that deviations are appropriately documented, tracked, and resolved in a controlled manner. To help you better understand the deviation workflow, we have included a detailed breakdown integrated with other QMS components.
3. CAPA management
Corrective and Preventive Action (CAPA) is the backbone of your quality management strategy. It represents a systematic procedure to effectively resolve incidents, deviations, and non-conformities, including finding their root cause, implementing adequate corrective actions, and preventing their recurrence.
4. Change control
It involves a systematic process for managing the changes made to a product or system to prevent any unwanted changes from occurring. A change control strategy aims to determine an action plan for system validation. In order to meet the overall quality requirements of a controlled environment, a requested or planned change must be thoroughly reviewed, fully documented, and authorized as soon as possible. However, from initiating a change control to creating an intuitive dashboard, creating a QMS on SharePoint helps you keep track of your change requests and collaborate more effectively.
5. Inspection (Quality Control)
Building adequate quality inspection checks has always supplemented the quality management process. So, how does it work? As part of the quality inspection process, several stages are involved, from pre-production to in-line and a final review after the product has been completed. Having a quality control procedure in place can help you detect errors early and maintain consistency throughout your teams, employees, and departments. Further, you can ensure the finished product meets your quality standards if you put quality instructions and processes together in a collaborative environment.
6. Document management and control
An optimized document management workflow is essential for organizations striving to achieve productivity goals. It comes without saying that employees who have easier and faster access to business-critical documents spend less time searching for them. SharePoint document libraries not only help you organize documents but also assist in sharing them with internal and external users for better collaboration. Apart from this, you can leverage easy check-in and check-out for flawless co-authoring, and many more SharePoint features for managing information, tracking document approval, automating document routing, and easing collaboration that form the core of your quality management strategy.Â
7. Audit management
How would you make sure that your efforts or quality guidelines match the set benchmarks? Auditing plays a crucial role in quality control. Although a time-consuming process, this step evaluates how well a quality management program conforms to company policies, procedures, and regulatory compliance. A quality audit involves various crucial steps like audit scheduling, creating audit checklists, executing audits, and generating audit reports timely.
Also, as a comprehensive process, auditing must be aligned with different quality management modules. However, robust document handling capabilities and automated approval workflows in SharePoint help you escalate NCs, CAPAs, and Risks and align them with the audit procedure, reducing the time and effort needed to pass an audit.
8. Training control
Employee training is essential to ensure that the employees are up to date with the organization’s current quality policies and procedures. Indeed, a robust QMS helps you align your employee training with your quality management strategy in a controlled environment. Streamlining training schedules, tracking training status, and ensuring effective coordination are the core functions performed by a QMS.
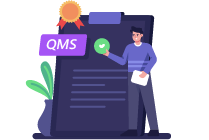
Want to streamline your quality management? Our QMS Buyer’s Guide offers valuable insights to help you pick the perfect solution and drive continuous improvement
Benefits of Quality Management Systems
Why SharePoint is the best choice to create Quality Management System?
No matter which QMS certification you are pursuing, SharePoint can help you build a QMS system to fulfill all your quality needs with flying colors. Everything is housed in an integrated system in a super-organized manner. It will also fulfill the management review and reporting requirements easily and quickly.
With the increasing adoption of the Microsoft 365 suite, it can be your best choice to satisfy QMS requirements. Read on to get a detailed overview of the SharePoint features that can be leveraged to create an efficient Quality Management System.
11 SharePoint Features You Need to Create a Quality Management System
1. A Centralized Documentation System
QMS involves various procedures, protocols, manuals, work instructions, and standard operating procedures to enhance the quality of the products and services within the organization. But simply having these documents is not enough, it is important to store these documents in an organized and easily accessible manner.
The inbuilt document management system of SharePoint serves this purpose by capturing, organizing, tagging, digitizing, storing, accessing, approving, and completing the documents automatically. The additional features like built-in version history, enterprise-grade security provided by Microsoft, and an automated document approval process are extremely helpful to manage and secure the documents effectively.
Document Management Features offered by BizPortals 365
Overview of Document Library
Document Approval System
2. Enterprise-Grade Security
Information is one of the most important assets for modern-day businesses. It is essential to secure the stored information and preserve the data confidentiality, integrity, and availability. To avoid security risks, SharePoint offers enterprise-grade security features provided by Microsoft. It allows a customized security system to provide user and role-based permissions at the library, site, folder, and even document level.
Library Permission Management
Document Permission Management
3. Detailed Audit Trail
Today, employees are working from multiple devices and locations and dealing with a constant flow of documents, and approvals. With all these variables, the importance of compliance has increased, especially in the manufacturing industry. An audit trail helps in getting a time-stamped and sequential record of the information. SharePoint proves to be a highly beneficial feature to track the document versions, date and time of document access, the name of the user who checked in or check out a document, actions taken with the document, comments, and much more.
Version History
Recent Activity
4. Audit Information Management
The management of audit information is important to ensure proper compliance. The audits have specific administrative purposes, such as auditing documents, performance, risks, and following up on corrective actions. As auditing is a mandatory requirement of a Quality Management System, it needs to be done very efficiently. With SharePoint, audit information can be managed with the help of customized document sets and lists. The audit information can be added as metadata and configured within the document sets to organize all the audit folders within the system.
Document Set
5. Automated Document Acknowledgement
As manufacturing processes are very lengthy and require a series of approvals. And the problem arises when users do not read the new policy updates and keep working according to outdated procedures. This is where document acknowledgment plays a crucial role. SharePoint offers automated approval and acknowledgment features with the help of Power Automate. It enables to create the custom approval workflows and capturing the acknowledgment responses of users in an automated manner.
Content Approval
Custom Approval Workflow
6. CAPA (Corrective and Preventive Action)
Corrective and Preventive Action (CAPA) includes a set of actions intended to improve the organizational processes and eliminate the causes of non-conformances. These actions are typically utilized in manufacturing businesses to fulfill compliance and regulations. Here, digital tools are very helpful in managing the process of CAPA. SharePoint helps in tracking custom lists with the help of Microsoft forms. It also allows customizing the lists in different views, colors, and metadata according to specific requirements.
Microsoft Forms
7. Display Knowledge Base Efficiently
To cope with the sheer amount of knowledge in the manufacturing business, it is important to reuse the existing knowledge base. The inbuilt knowledge base of SharePoint QMS helps in creating and formalizing the knowledge, creating the basis for smart manufacturing, and supporting the production system. Site pages solve this purpose efficiently. It creates dedicated pages to create a knowledge base in SharePoint. With this page template, you can easily embed diagrams, project-related documents, and collaterals, add metadata, and much more.
Overview of Knowledge Base
8. Logging Change Requests
Change is an inevitable part of business procedures but it is important to track the changes and ensure that they do not impact business activities negatively. A Quality Management System manages the change request and tracking mechanism in a streamlined manner. Here, the Power Apps offered by Microsoft can be very helpful in capturing the details of change requests and storing the information in relevant SharePoint folders. It does not only log the change request but also reviews them after implementation to verify the completion of the required changes.
9. Customer Feedback
Every business is eager to improve its business processes, product, and services. So, they decide to gather customer feedback and store the information in SharePoint along with basic order details. And the easiest way to gather and store customer information is through Microsoft Forms. The information can be stored in SharePoint custom lists to access them anytime, from anywhere.
User Response Collection
10. Efficient Tracking of Metadata and Automated Notifications
Data quality starts with the effective management of metadata. It provides the necessary definitions and documentation to ensure that data is understood and consumed properly across the organization. Quality Management System maintains specific information such as expiration dates of policies and procedures. SharePoint helps in tracking and managing the metadata within the document library to keep the information always up-to-date. In addition, the user notifications can also be automated with the help of customized SharePoint workflows to ensure that the information is communicated to the relevant users.
Library with metadata
11. Enables Effective Internal Communication
The complexity of communication has increased drastically with the emergence of varied communication platforms. With the rise of digital transformation, businesses are finding new tools to drive internal communication success. Here, SharePoint plays a key role to build dedicated communication sites and leveraging communication channels like Microsoft Teams, Yammer, and Outlook email within the SharePoint intranet.
Teams
Project Site Discussion Forum
Start leveraging SharePoint QMS with BizPortals 365
At BizPortals 365, we have years of experience building next-gen SharePoint Quality Management Solutions. Moving from conventional Excel spreadsheets and offline files into SharePoint provides great control of data, greater visibility, and enhanced workflow capabilities to manage business processes efficiently.
Table of Contents
- What is a QMS?
- How QMS is beneficial for your business?
- Benefits of Quality Management Systems
- Why SharePoint is the best choice to create Quality Management System?
- 11 SharePoint Features You Need to Create a Quality Management System
- Start leveraging SharePoint QMS with BizPortals 365
Step into a smarter digital workplace
Get a Free Product Tour